1978 R100RS Burning Through Fuses
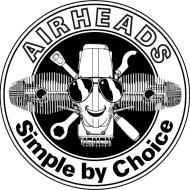
Hi all, I've got a bit of a (personal) stumper here, but I'm certain someone with more experience will know what to do.
About two weeks ago I bought a 1978 R100RS (pictured, and yes, it's definitely not an unmolested example) from a private seller near me, and since buying it there has been one major problem: it keeps blowing the turn signal/brake light/horn fuse. Obviously, replacing the fuse continually is not a solution. I've tested several scenarii to try and determine the source of this problem.
- Firstly: it has never blown when I've used the horn, or the brakes; only when I've had the turn signals active.
- Secondly: it has never blown a fuse when the engine was not running (e.g. I can turn the key on and run the indicators almost indefinitely, but have not deleterious effects on my fuses).
- Thirdly: It's not super clear what the other conditions leading to the blown fuse are. I have ridden it for hours and had no issues, and I've ridden it for less than a minute and had the fuse go on me nearly immediately. I thought it was related to a bumpy ride, but then had the fuse blow on a smooth street. I thought it was from the combination of both the turn signals and brake indicator being on simultaneously, but then the fuse blew when I just had the indicator on.
- Fourthly: There was an aftermarket, 3-prong turn signal relay in place when I bought the bike. I thought that might have been the culprit (given that this only happens when the signals are engaged), but replacing the relay and cleaning up all the wires did not solve the issue.
The motorcycle has had a fair amount of work done to it across the decades and its multiple owners. It's been modified to resemble an 'S', has Dell'orto PHM 38B carbs, no air box, and a host of other small changes, but those wouldn't affect the electrics. The big thing that I think is pertinent to this situation is the prior owner changed from the stock charging system to an Enduralast system (the 450-W EDL4, I believe) just before I bought it. I'm not certain how this would affect the circuit inclusive of the signals, brake light, and horn (especially when it's only been the signals that have blown the fuse), though.
Have any of you seen this happen before, or perhaps some guidance related to years of experience? Luckily I can mainly avoid using the indicators: hand signals work, and, as I said, neither braking nor horn use have led to this outcome before, but I'd like to solve this issue, rather than continually step over a 'missing stair'. I'm hoping I can take care of this without too much heartburn.
If you have an idea of what it could be, but I've neglected an essential piece of information, please let me know. Thanks in advance!
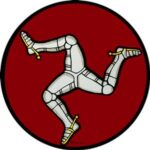
STARTING POINT
1. First off we'll have to assume you are using 8A fuses and not something lower, like 6A. The BMW wiring design only has the two fuses and that puts a heavy load on both branches of the harness.
2. Secondly we assume the 2 fuses are in the stock fuse location within the headlamp shell, and have not been "remoted" to another physical location as was popular back in the 1980's.
3. Next we need to assume that you have already fully investigated that a wire is not being pinched inside the headlamp shell when the HL reflector and rim is offered to the headlamp bucket. Nor is the rear of the headlamp bulb touching the fuse holders or any part of the multi-colored circuit board inside the headlamp shell (which can happen with LED H4 bulbs). This includes wires in and around your new flasher unit.
4. Finally the new flasher unit is not drawing more than 8A simply to operate. And that all connections to this unit were made in a professional manner, and that any unused terminals were insulated with heat shrink tubing to keep them out of trouble.
INVESTIGATION
1. The place to start you investigations is with ANY home wiring. ALL HOME WIRING IS HIGHLY SUSPECT. People (owners and most mechanics) are generally idiots about electrical wiring and clueless about what it takes to survive on a motorcycle. All connections should be made with connectors or 100% soldered and then covered by heat shrink. ABSOLUTLY ZERO electrical tape, wire nuts, or any other wiring devices common to "home wiring". No new wiring made with anything less than 16AWG multi-strand automotive type wire. No solid core telephone cable or lamp cord. In short, if it doesn't look like it belongs under the hood of a new Toyota, then it doesn't belong on your motorcycle.
2. Start with a systematic search that follows a LOGICAL flow. You'll need to look at EVERY single part of the turn signal system, which starts with complete disassembly of EACH of the 4 turn signal pods, inspecting the bulbs, and then the bulb sockets, then the wires within the pods... working your way back toward the headlamp shell. Any place the 4 turn signal pod wires make sharp bends around metal edges, or can get chaffed is suspect. You may find suspect places where rubbing is occurring and ALL of those should be coated in heat shrink.
This work is not much fun and calls for rigorous and VERY intense inspection of every inch of wiring. But it's the only method that will allow you to relax while you're out riding. Do the close inspection and hard work at home, and you won't need to be making those "can you bring the trailer and come pick me up" type phone calls.
And again...
• Use a logical flow. Don't jump around from the handlebar switch to the battery, to the right rear TS lamp. Start at the individual rear TS pods and work toward the headlamp bucket where the wiring for all 4 TS pods come together at the multi-color board. Then to the handlebar switch, then to the flasher unit, etc.
• Use common sense. If you find a fault (for instance) in one rear TS pod from rubbing, then it stands to reason that the exact same issue is occurring in the other rear TS pod. So in the name of prevention, fix them BOTH !
Owning an old Airhead is easy.
Keeping an old Airhead running great is the true test.
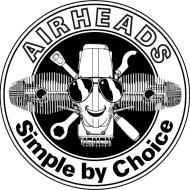
Thanks @wobbly! I'll cover the axioms, and then move on to any other details. I haven't had an opportunity to work on it today, but should have time this week with the pending holiday to set a few hours aside to chase down gremlins.
- I am using two, 8-amp, GBC/Continental/Torpedo/Bullet/&c. fuses.
- The two fuses are in the stock fuse location within the headlamp shell.
- I have looked for pinching and unwanted contacts in the headlight bucket and haven't found anything. It's a bit difficult to prove a negative in this case, but everything looked to be in order. Are there any trouble spots that look like they shouldn't be a problem?
- The new flasher is a new OEM module from a reputable source, and so I'll admit that I did not check the relay's operation. That being said: all pins were attached according to the wiring diagram in the Haynes manual, and using spade connectors. The wires were not connected to the original plug, though. There were no unused terminals.
From there, I'll commence the search, heat-shrinking along the way. Thank you for the advice, and for the wiring diagram: I appreciate it. I'll be certain to follow up with what I find. I plan on taking lots of photos, and if I find something interesting, I'll document it.
Cheers!
-Thomas
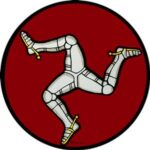
► Intermittent shorts are the hardest to find. They are usually caused by a chaffed wire that is occasionally touching grounded metal at a sharp bend or metal housing entrance (such as where the 2 front TS wires exit their TS pod stem, or where they enter the headlamp bucket).
► There should be rubber grommets where ALL wires enter the HL bucket. Quite often the grommets have disintegrated over the last 40 years and simply need replacing. A large grommet selection and a can of spray silicone can really help. The silicone makes old grommets supple again, and can also lubricate harnesses that are being inserted through new grommets.
► A technique I have used is to replace the fuse with an analog DC ammeter. While the system is ON and operating, the meter will show the normal current draw. Then proceed along the length of the harness, wiggling and tugging it, while watching the meter. When the general area of the short is discovered, the ammeter will "peg out". Always be ready to immediately turn the key OFF to prevent any damage. By (ab)using a meter in this way, you won't run through $30 worth of fuses.
Built in 1971, this simple test meter has earned me at least $20,000
► All this harness investigation will undoubtedly call for some connector unplugging along the way. Never miss an opportunity to improve the system performance by adding an anti-oxidant paste to each connector before re-connecting it. (Such an anti-oxidant compound would be No-Ox-Id.) In fact, when electrical issues baffle me, I simply go on the defensive and begin to implement preventative measures. In the course of doing that work I typically stumble over the root cause of the initial problem!
[Side Story: I've had customers offer profuse thanks, vigorously shake my hand and call me a genius for fixing their electrical problem. I'd simile and think, "I'm charging you $200 for 15 minutes work and $1 worth of commercial wiring components to correct a problem you created when you added XXX using packing tape and wire from your kid's broken Play Station. This is too easy." ? The point is, when you own a motorcycle with 10 previous owners, you're bound to meet this same guy.]
Hope these ideas help.
Owning an old Airhead is easy.
Keeping an old Airhead running great is the true test.
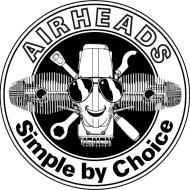
@wobbly So far, no joy, but it's been fun going through, cleaning everything up, adding heat shrink, etc. I ordered some of the No-Ox-Id -- took a while for it to get in, but I now likely have enough to last through the rest of my life -- and spent a couple hours yesterday going from the turn signal pods 'upstream'. I found some chafe points in the housings, themselves, and cleared those up, but no amount of wiggling the accessible lines led to the fuse to pop. My multimeters are not built to handle the currents I'm expecting, so I'm going to find a local lab supply company (or go online if I can't) to pick up an old-fashioned panel ammeter for cheap.
Some of the more egregious points were within the rear steel bar joining the two pods. The bar was also slightly bent, and so I took it off, cleaned it up, evened it out, added tubing to relevant hotspots, and then put it all back together. The issue remains: if the bike's engine is off I can turn on the turn signals to my heart's content and leave them on indefinitely, but if the bike is running (even at idle) it pops. Sometimes it pops after a few flashes, but sometimes I can use it for a few turns before it goes. I'm still not certain of the exact failure condition, but with every ride, and every bit of maintenance I do, I feel like I'm at least getting closer. It also seems most likely to go early in a ride. If I've been riding 10 or so minutes I seem to have some ability to use the indicators, but if I've just started the bike, the fuse is much more likely to go as soon as I try it.
I think my next big step is to remove the tank and take a good look at all that wiring underneath. I'll probably refresh the brake fluid whilst I'm at it (being careful of its corrosive nature). I have found a couple spots with splices that look to be underrated for the amperage, and I plan on removing and replacing those. I also unwrapped a ball of electrical tape that was holding the (defunct) signal buzzer. I say defunct, because it looks to have been wired to a permanently-off condition (ideal, honestly).
Anyway, no major update, but I figured documenting some of what's been done as I do it might help someone else in the future, too.
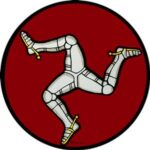
Thoughts....
> Fuses blow for 2 reasons: Load and Shorts. Your specific condition sounds like it's one where the "load" is too high for the fuse, rather than a direct "short circuit".
> Non-standard items added to the circuit, like your turn signal beeper (or the wiring to it), may be drawing too much current. That beeper would definitely qualify as a home-brewed item and thus not to be trusted. Not only should the beeper be completely removed, but all the associated wiring to it should also neatly disappear. Especially if you are not using it, please take it back to stock. The beeper may have been great at one time, but may now be filled with water. Fools do stupid stuff like taking the beeper off a defunct computer, never thinking about the fact it was never designed to get wet.
> Why are you waiting until now to remove the tank? The wires from the TS pass through the main harness which travels along the backbone of the frame. I have seen many bikes where the rubber mounted tank (which moves as the bike vibrates) scrub a hole in the harness and make intermittent connections. When I urged you to inspect every inch of wiring in a logical sequence, that included inspecting the 6 feet of wiring between the tail lamp housing and the head lamp. Based on what you have said about not removing the tank just yet, your inspection procedure is far too lax.
> There is also a harness connector and relay behind the LH side panel that will need all the terminals coated in No-Ox.
> While you have the tank off is a good time to inspect the Starter Relay which sits in a relay socket on the LH side, just beneath the brake master cylinder. Corrosive brake fluid dripping onto that relay is a CONTINUAL source of electrical problems for 1978 to 1980 owners because ALL electrical power passes through that relay and its socket, as per the cartoon below....
I am not chastising you to embarrass, but rather to educate that your inspection procedure needs lots of improvement. You will need to work your way along the harness to touch AND visually inspect every inch of wiring. Lax inspection will never discover lax wiring issues, because as Albert Einstein famously noted, "We can't solve problems by using the same kind of thinking we used when we created them."
Let me encourage you to "step up your game". Happy new year !!
Owning an old Airhead is easy.
Keeping an old Airhead running great is the true test.
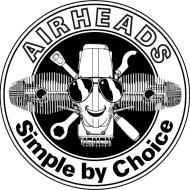
@wobbly I honestly appreciate the advice and am not embarrassed: I came here looking for help, and know that I currently know little regarding these machines and best practices regarding their diagnosis.
The turn signal buzzer was a stock item in 1978, hence I didn't remove any of the present wiring (it seems to have been a short-lived option). It looks like a prior owner removed the buzzer, itself, but left the relay in place. I'll do some more model-specific digging to see if there are any unexpected 'gotchas' in pulling the relay from its plug, or even removing that bit of the harness and splicing the connections together, but I somehow get the feeling that the latter path will lead to stray, unconnected wire ends that I'll have to manage somehow.
I hadn't yet removed the tank for two reasons: one, because the failure condition seems related to the engine running, and two, because I've never removed a motorcycle tank before, and I wanted to wait until I had a several-hour span when I could take care of that without interruption: projects, especially unfamiliar ones, always expand beyond the original amount of time alloted them. I started my inspection at the rear of the bike and worked up to the tank; I also looked at the front pods, working back to the stem, all of which seemed a logical order before moving to the junction under the tank.
Again, thanks for the advice and recommendations.
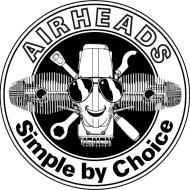
@wobbly I'm not much of one for new year's resolutions, but 'stepping up my game' seems a good one. Happy new year to you, too!
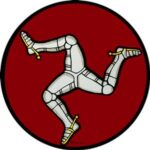
@thomas-schratwieser All noted and appreciated.
It's not that Airheads are hard to work on or that the task is overly daunting. I have worked on numerous motorcycle brands and I find the Airhead to be very straightforward, highly organized, well thought out, and thus easy to work on. It's the systematic approach to troubleshooting that gives most people the "fits".
If the operation is: proceed to porch, approach door, turn door knob, go inside.... then most people might approach this as: go inside, proceed to porch, turn door knob. I've often thought that computer programmers might make the best mechanics simply because they recognize the sequence and organize accordingly.
Anyway, the main thing is that you're on your way !
PS. The best way to secure unused factory leads is to completely cover the wire end with heat shrink, connector and all. This way if you want to bring that function back, all you need to do is cut off the shrink. Until such time, there's no chance of it making a wayward contact.
Owning an old Airhead is easy.
Keeping an old Airhead running great is the true test.
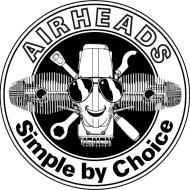
@wobbly Your gentle admonition spurred me to take the afternoon off and go outside to remove the tank and look under it; it was significantly easier than I was expecting, and I wound up (so far) successfully solving my issue. I continued to wiggle all the cables and found no fail state as the signals were on (I waited for the lamp to actually be illuminated each time). There was no sign of corrosion from brake fluid, and the read lead paint under the front brake reservoir was in good shape. I'm not certain if it came painted that way from the factory, or if a prior owner thought to do it, but it looked good. Many connections needed to have their old tubing removed and to be refreshed, but it was the new voltage regulator/rectifier that seems to have been the source of my problem.
I mentioned before that the prior owner had recently replaced the charging system on the bike: well, the ground strap for the new box had been omitted. I ran an overgauge wire from the rectifier to a clean point on the frame, and did the necessary wire management that goes along with it. I then remounted the tank and started up the bike. The indicators didn't fail, so I rode around in my neighbourhood for about 10 minutes, turning (and signally) at every chance I got and trying to cause a failure. So far, so good. I then removed the signal buzzer relay and sealed the connector to see if there were any ill effects; none so far, so I'll probably just remove that entirely next time I spend a day doing maintenance.
Again, I appreciate your advice and recommendations!
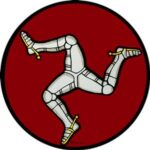
Frames carry the engine. Copper wire carries the electricity.
Congrats on the find ! It's just like I said... When you loose the trail of the beast you're hunting, if you'll go on the defensive and start massaging other bits you'll often stumble over what you were initially looking for. Good find !!
However, I remain a bit perplexed as to what you were looking at. There is no "rectifier-regulator". These are 2 discrete functions accomplished on the stock Airhead by 2 individual units....
>> The rectifier is a large, open circuit board inside the front cover of the engine. It does indeed need a return ("ground") wire because it's attached to the cam chain cover and the fact that there is a paper gasket separating that cover and the engine, plus rubber rectifier supports, often creates a requirement for a wire to jump between the cam chain cover and the engine proper.
Now, because the 4 OEM rubber mounting standoffs often create issues of their own, for some time now it has been standard practice to replace the 4 rubber rectifier mounts with solid metal versions. (Motorrad Eliktrik sells these.) Simply installing the metal standoffs will sometimes negate the need for this jumper wire, but not always. You can give the metal standoffs a HUGE assist if you will simply apply your No-Ox-Id to both ends of the 4 standoffs AND both ends of the ground wire. (Never miss and opportunity to use your anti-oxidation compound, because after 40 years on the road there is no shortage of oxidation on the motorcycle !!)
>> The voltage regulator is a small, sealed canister, on the RH side of the frame, just under the brake master cylinder. The unit has a 3-pin connector on the bottom, and these 3 pins should have No-Ox-Id also applied to them. One of those 3 contacts is a Brown wire, which is harness Return ("ground"). So no extra wire is required there. (However, what is a mandatory requirement is that the dash board "Gen" lamp illuminate every time the ignition key is turned ON. The resistance of the working bulb is an integral part of the Airhead charging circuit.)
Now, having said all that, let me explain why your repair may be short-lived. The motorcycle frame is the very WORST place to attach a Return wire for the very fact that the frame is Steel, and steel will Rust when exposed to water, and Rust is an electrical inhibitor. Oh sure, it's working Now, but over time as the rust develops the quality of the connection will slowly degrade. Often times so slowly that you don't notice that (some months later) your bulbs are running on 10V instead of 14V, or that your maximum battery charge current is 1A rather than 3 or 4A.
The BEST place to attach a Return ("ground") wire is where BMW did, which is the LH ignition coil bracket. There are 2 bolts on that bracket, and the front one should already have the harness Brown Return wires attached there. (The coil bracket is plated, and thus corrosion will be held to a minimum.) Now, of course you can help yourself and the electrical system in a HUGE way by removing that front bolt and coating the entire bolt (threads and all) with No-Ox-Id. Then, if you need a good frame attach point, the rear bolt (once coated with No-Ox-Id) is there waiting for you.
(Are you starting to see a recurring theme concerning the anti-oxidation paste ? ? )
Hope this helps.
Owning an old Airhead is easy.
Keeping an old Airhead running great is the true test.
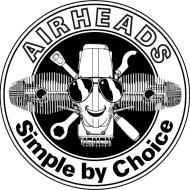
@wobbly Thanks! I'm happy that it seems to be behaving, and that I got a chance to do some preventative maintenance on a lot of the other wiring. I think that little tub of No-Ox-Id will be used (or immediately available) every single time I work on the bike.
I was also a bit perplexed regarding the regulator. The upgraded charging system is a plug-and-play system (Enduralast EDL4 https://www.euromotoelectrics.com/product-p/edl4.htm), which is a brushless, permanent-magnet rotor. It also has a replacement regulator, which combines the function of the rectifier and regulator in one (I'll refer to it as the R/R from now on). I haven't taken the timing cover off, yet, but when I do, I believe that the diode board will no longer be there, or, if it is, it will be completely disconnected: a vestigial remnant. This R/R replacement box apparently also removes the no-charge condition for a burnt-out warning light, as well, but I'll be keeping an eye on the light when I turn on the bike, anyway, because I don't want to necessarily put complete faith in that.
Ah, the changes you find on a multiple-owner machine.
On the R/R, there is a case ground point, an icon indicating its which you should be able to see on the left-hand side of the box under the mounting point. It is 'recommended, but not required', which I suppose means that its new mounting bracket might provide the necessary connection to the frame, but does not seem to have done in my case.
I didn't realise that the LH coil bracket was the original location, but I will absolutely move the connection to that point when I next have the tank off. I'll probably go ahead and do that this weekend when I have the time and daylight. I saw a couple splices with a too-low gauge connector, and wanted to replace them with an appropriate splice.
Again, thank you so much for your advice, recommendations, and the time you've spent writing back and forth.
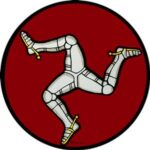
Posted by: @thomas-schratwieserOn the [rectifier-regulator], there is a case ground point, an icon indicating its which you should be able to see on the left-hand side of the box under the mounting point. It is 'recommended, but not required', which I suppose means that its new mounting bracket might provide the necessary connection to the frame, but does not seem to have done in my case.
I didn't realise that the LH coil bracket was the original location, but I will absolutely move the connection to that point when I next have the tank off. I'll probably go ahead and do that this weekend when I have the time and daylight. I saw a couple splices with a too-low gauge connector, and wanted to replace them with an appropriate splice.
► Again, let me quote the basic rule of wiring motorcycles....
Frames carry the engine. Copper wire carries the electricity.
Obviously the previous owner did not believe this, but now you have proved it to yourself. Yes, I am familiar with this type rectifier-regulator, I was simply unaware they had made it to the Airhead world. An interesting test would be to rev up the engine (to say 3000 RPM) and take a voltage reading across the 2 battery terminals. That will show the "charge voltage", which is different for the various types of batteries.
► The LH coil bracket is where the stock harness contacts the "frame" for the purposes of Return. You should see 3 Brown wires going into 1 "ring lug" at that location. If you do not, then I'd certainly like to know where this junction has been moved to, because it MUST exist.
Keep up the good fight !
Owning an old Airhead is easy.
Keeping an old Airhead running great is the true test.
- 27 Forums
- 1,924 Topics
- 10.9 K Posts
- 0 Online
- 6,018 Members