Sheared Flywheel Bolts to Crankshaft - Repair Options
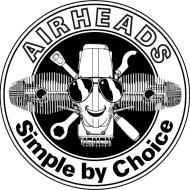
Hello!
I've been piecing together a 1976 R90 (50 K miles) basket case for a few months now and had the bike completely assembled. Upon firing it up, I noticed a loud knocking sound from the engine and went about trying to diagnose the problem. Since this is my first airhead, I really didn't know where to start so I went about checking and replacing items that were worn beyond specification with the help of Snobum's articles and the Clymer manual. I replaced rod bearing journals (even though they looked and measured good), timing chain and sprocket (cleared up the double image on the timing mark), re-built carburetors, adjusted valves. The crankshaft had no noticeable play in in it that I could tell. No piston slap marks either.
Noise would not go away and I did not want to ride it until the problem was fixed out of fear of destroying the engine.
After all repairs mentioned above, I was in the middle of trying to diagnose the sound origin when the engine seized up at idle. After a night of stewing, I checked the timing window and saw the flywheel teeth through the timing window. Disassembly confirmed that the flywheel had come off of the crankshaft.
Somehow the flywheel bolts had backed out of the crank and the knocking sound (I'm assuming at this point) was coming from the loose flywheel and bolts. There were some sheared pieces of the bolts still in the crankshaft tapped holes.
Here is a link to a picture of the crankshaft end: https://www.dropbox.com/sh/hi1ds7ku9u66pkq/AADvDJQnC4LxujvvEPb4YhnRa?dl=0
My question has to do with how to repair.
I think I have 2 options, but would like to hear what the experts here have to say:
Option 1: Replace the crankshaft and flywheel. Complete engine teardown and assembly are the only drawbacks here + the cost of new bearings and crankshaft. The upside is that I have a new bottom end to go along with all the other re-builds I have done on the bike. I feel like I can do most of the work here, but I would need a recommendation for a trusted shop in South Carolina that can press in the bearings.
Option 2 : Extract the sheared bolts while the crankshaft is still in the crankcase and clean up the face of the crankshaft. Is this an option????? Understood that I need to check if the hidden thrust washer has come off its pegs. My concern would be damage to the crankcase while repairing the crankshaft in this manner. The threads appear to be in good shape. However, even if the torque can be achieved on the flywheel bolts, my concern is that the holding frictional forces between flywheel and crankshaft might be reduced due to the reduced surface area.
Thoughts, opinions, suggestions are definitely welcome and appreciated!
Thanks!
Jason
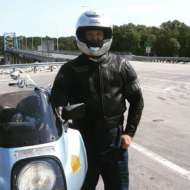
Ouch. While I'm no expert, it appears that the crank end and flywheel bolt holes have extremely tight tolerance bores to minimize any movement. You'd have to repair the bolt holes in the flywheel or I'm afraid this would happen again down the road.

I'm no expert, so consult the Snowbum files on this detail, but I believe the power of the R90 uncovered the "weak flywheel bolts" issue. These bolts had been OK on the R60 and R75. So later model R90's and all R100's were fitted with more substantial flywheel bolts.
Since the crankshaft wasn't chocked, I think it's safe to assume the hidden thrust washers are no longer in the correct place. You can always remove the oil pan and verify.
Swapping out the crankshaft doesn't necessarily mandate new main or rod bearings. That is done based on the bearing and journal diameters. These engines have massive main bearings and adequate oil filtration, so unless the bike has 100K miles or higher it's probably not needed. And then too, you just put a new set of rod bearings in, so why would you need more new bearings there ?
If you are in western SC, there is a great shop near Athens, GA called Boxerworks that can probably supply the later model crank, flywheel, and make the necessary measurements. The owner has 30+ years on Airheads and is the GA state Air Marshall. You could do worse.
Hope this helps.
Owning an old Airhead is easy.
Keeping an old Airhead running great is the true test.
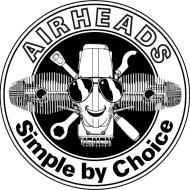
Thanks for the reply, thundermotive!
Yep. I'm pretty bummed about the failure, but hopefully this is the source of my knocking sound and after fixing it, I'm done!
There appears to be a small clearance bore for the bolts to get to the threads in the crankshaft and the manuals/sources/forums I have read indicate that the torque is transmitted through the friction between the flywheel and crankshaft end.
So it seems that the torque is not being transferred through the bolts and clearance is not so much as an issue as achieving the required torque on the bolts. That's why I was hoping a repair with the crankshaft in place would do the trick.
Or maybe I'm wrong here?
I'm thinking that a crankshaft replacement will give piece of mind either way....just a lot of (more) work.....
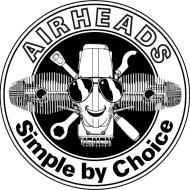
Thanks for the reply, Wobbly!
It appears that I have the late model crankshaft for the R90. It seems to be the same as the R100 models as you said.
I tend to agree with you on the thrust washer. I'll check.
Agreed on the bearings. No new connecting rods bearings would be needed. I'm just wondering if I should go ahead and replace the main bearings while in there? Much of the bike's other bearings and wear items have been re-built/replaced at this point. However, since it is a matter of dimensions, I'm tending to agree that I should just just check the main journals and the current bearing and if the clearance is within tolerance, I should just roll with it and rely on the standard longevity of the bottom ends of the airheads.
Thanks for the recommendation on Boxerwerks. Unfortunately, I'm in the eastern part the state in Charleston, SC about 4 hours from Athens so something a bit more local would be preferable. That said, I'll go there if that is needed to get the job done! But if I'm just measuring the journals of a new/used crankshaft and bearings at this point, I'm thinking I can get a decent machine shop to do the measurements or?
Thanks again!

It appears that I have the late model crankshaft for the R90. It seems to be the same as the R100 models as you said.
Well, you're in luck then !
The broken bolts will have pushed up small divots of metal around the holes on the crank and flywheel. Those have to be removed so that the flat surfaces of both parts can come into full contact for the reasons you explained. You can do this with the crank in the engine using a small abrasive handheld stone, like ones used to sharpen pocket knives.
The bolts you have must have been seriously over-torqued, probably using an air impact wrench. To properly do this job you have to chock the flywheel so it can't rotate, then tighten new bolts to the specified torque with a handheld torque wrench. (The problem here is not torquing the bolts, but holding the flywheel stationary.)
I tend to agree with you on the thrust washer. I'll check.
I simply know they can fall out; I do not know their propensity to do so. Nor do I know if they can be re-situated from the sump cover access point. I know it's better to be safe than sorry.
Agreed on the bearings. No new connecting rods bearings would be needed. I'm just wondering if I should go ahead and replace the main bearings while in there? Much of the bike's other bearings and wear items have been re-built/replaced at this point. However, since it is a matter of dimensions, I'm tending to agree that I should just just check the main journals and the current bearing and if the clearance is within tolerance, I should just roll with it and rely on the standard longevity of the bottom ends of the airheads.
Unless you rebuild engines for a living, you probably can't measure this yourself. The difference we are discussing is the oil film thickness !! You haven't stated the mileage on the bike, but the far, far safer way is to let sleeping dogs lie for now. Then, when the bike is back on the road you can accurately assess that clearance using a simple oil pressure test. With new rod bearings, any lack of oil pressure has to be the size/condition of the mains. Think about that !
Thanks for the recommendation on Boxerwerks. Unfortunately, I'm in the eastern part the state in Charleston, SC about 4 hours from Athens so something a bit more local would be preferable.
Then you'll simply need to move. 😛
Just kidding. Contact your Air Marshal.
Owning an old Airhead is easy.
Keeping an old Airhead running great is the true test.
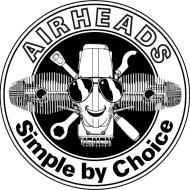
If it were me, I'd post question on airlist. Either Tom Cutter or Snowbum are likely to answer. They both can be trusted to give good information.
Bob
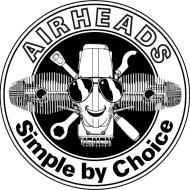
If it were me, I'd post question on airlist. Either Tom Cutter or Snowbum are likely to answer. They both can be trusted to give good information.
Bob
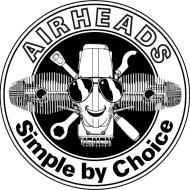
Thanks, Bob. I've registered with Airlist and hopefully I'll get approval to join and post soon.
Jason
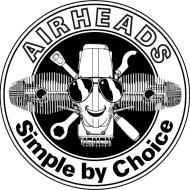
Thanks, Wobbly!
I measured the length of the crankshaft that extends from the visible thrustwasher (A) and then compared that the to depth of the mating recess on the flywheel (B). According to Snowbum Article 60-2, (A) should be greater than (B), but my dimensions show the opposite. (B) is greater than (A) by about a little less than 3 mm so this confirms that the Thrust Washer has slipped off its pegs!
This changes my options a little.
It looks like I will need to disassemble the engine in order to properly seat the hidden washer. Given this, the following questions come to mind:
1. Is there a way to seat the washer without dis-assembly?
2. With disassembly, should I just go ahead and replace the crankshaft with a good used crankshaft? I can compare journal measurements and make changes in main bearing selection (if necessary) accordingly. Plus, no divots and threads should be good.
3. Or, with disassembly, is stoning of the current crankshaft to even out the divots and extraction of the sheared bolts a better option?
To be honest, I am not keen to change out crankshafts since the current one seems solid with good oil pressure (according to the oil pressure gage) and as a result has good clearance in the main bearings. But with a replacement crankshaft, I should be getting good journals (after confirmation) and good threads on the crank end (also after confirmation).
I'm also not keen to go to Athens for repair since a certain rival of ours hails from there.....Go Jackets!
By the way, is there a link for installing a pressure gage on the bike?
Thanks for the feedback so far! Really appreciated!
Jason
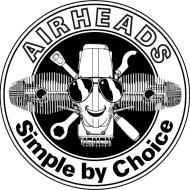
The smiley face should be the dimension "B".

Jason -
Ahh, a Tech man ! That's good ! I got some Tech stories, but that's for another day. BTW... the shop is actually in Watkinsville and there is not even a trade school in that town. 😛
I'm all for using what you have, partly from my conservative nature and partly from experience. You know all about the crank, all the history, and know it fits. But just as Murphy predicted.... you're installing the last bolt on engine re-assembly when you discover that the new crank is missing some required feature because it's actually from a slightly different year model. :angry:
Therefore, I'd start with trying to get the broken bolts out. Hopefully no LocTite was used and they will spin right out. If you need to use an Easy-Out, then the problem of crank rotation comes into play. So the bolts become the determining factor, no matter how you feel about the issue.
If the bolts can be extracted, then research if the thrust washer re-installation. Seems to me if they can fall out, then they can be re-installed through the engine sump. You may have to work with special lights and dental picks, but that's still better than complete engine dis-assembly. Once the thrust washers are in place, insert a small chunk of 2x4 under the front engine cover to push the crank rearward and hold them.
The oil pressure gauge is fitted in lieu of the oil pressure sender switch. There are two thread patterns, so you'll need to pull the switch to find out which one you have. Then make an extender/adapter to allow the gauge to attach at that location.
Hope this helps.
Owning an old Airhead is easy.
Keeping an old Airhead running great is the true test.
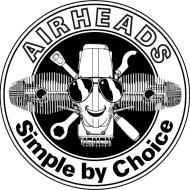
Hey Wobbly:
We'll have to swap Tech stories when we meet up at some point! I've got too many (good, bad, and ugly).....
Too funny on the Trade School reference. Haven't heard that in a while, but I think I still have my old North Avenue Trade School shirt buried in a closet somewhere.
Even though the Holidays have settled in, I was able to get the sheared bolts out. A homemade drill bushing came in handy with keeping the drill from walking and bolt extraction was surprisingly easy afterwards. Looking at the bolts and the way they necked down, it looks like they were over-torqued during installation as you mentioned.
I took off the right cylinder and it looks like the washer is still on the pegs!
Picture is in the following link: ?dl=0
Problem is that the crankshaft has definitely moved forward and separated from the thrust washer.. Pushing on the rotor by hand does not seat it back in place. Crankshaft does turn freely and easily with allen wrench at rotor.
My questions then are as follows:
1. What's the best way to pull the crank back to the thrust washer? I can see 2 options: Install flywheel and just have the bolts pull the crank back in place or remove rotor and tap on crank nose with rubber mallet.
2. Since I cannot push the crank back by hand, Is there a possibility that there is damage elsewhere that I need to check on?
I plan to stone the face of the crank to take out the divots tomorrow. New bolts arrive Friday so hopefully I have solution in place by the end of the weekend......I know....finger crossed on that and I'm sure Murphy will show up at some point to drive me to drinking at some point!
Thanks again for the help!
~ Jason

Jason -
Sorry, I really can't answer your question from direct experience. From experience building (non-BMW) twin cyl motorcycle engines, the crank should NOT slide back and forth simply by hand pressure. However, you should be able to easily move it to the rear once a 14-18" pry bar is located in a safe place through the cylinder opening. Only 1 or 2 pounds of pressure is all that should be required. Once the crank moves to the rear, you can place a small chunk of 2x4 on the alternator rotor, re-install the engine's front cover, and gingerly tighten the 2 cover bolts to hold everything (thrush washers, crank, 2x4) in position.
The crank shaft should not turn freely since you still have the opposite spark plug still in place AND the pressure of that cylinder's valve train. And be careful about using the alternator bolt to turn the crank... they can loosen.
I don't suspect damage is causing a problem, but I always suspect that some thrust washer or other piece of hardware is not exactly lined up like it wants, so that the crank can easily slide into place. Gilda Radner was right... "It's always something." Go slow, use lots of light, and apply slow steady pressure. Prayer certainly helps.
When you get as far as the flywheel re-install... How will you hold the crank from rotating ? Do you have a toque wrench ?
Owning an old Airhead is easy.
Keeping an old Airhead running great is the true test.
- 27 Forums
- 1,812 Topics
- 10.3 K Posts
- 1 Online
- 5,564 Members